Discover What is Porosity in Welding and Its Impact on Structural Integrity
Wiki Article
Recognizing Porosity in Welding: Exploring Causes, Results, and Avoidance Techniques
As experts in the welding industry are well mindful, comprehending the causes, effects, and prevention strategies connected to porosity is essential for achieving durable and reputable welds. By delving right into the origin creates of porosity, examining its harmful impacts on weld quality, and exploring effective prevention strategies, welders can improve their understanding and abilities to produce top quality welds continually.Typical Reasons For Porosity
Porosity in welding is primarily triggered by a combination of elements such as contamination, improper securing, and inadequate gas coverage during the welding process. Contamination, in the type of dust, grease, or corrosion on the welding surface, develops gas pockets when heated, leading to porosity in the weld. Inappropriate protecting takes place when the shielding gas, typically made use of in processes like MIG and TIG welding, is not able to completely shield the molten weld swimming pool from reacting with the bordering air, causing gas entrapment and subsequent porosity. In addition, insufficient gas protection, often due to incorrect circulation prices or nozzle positioning, can leave components of the weld vulnerable, allowing porosity to form. These aspects collectively add to the formation of gaps within the weld, deteriorating its honesty and potentially creating structural problems. Comprehending and attending to these common reasons are crucial actions in preventing porosity and ensuring the quality and strength of welded joints.Effects on Weld Quality
The presence of porosity in a weld can dramatically jeopardize the total high quality and honesty of the welded joint. Porosity within a weld creates gaps or tooth cavities that damage the framework, making it much more susceptible to fracturing, corrosion, and mechanical failure.Moreover, porosity can hinder the effectiveness of non-destructive testing (NDT) strategies, making it testing to discover other issues or gaps within the weld. This can result in considerable security worries, especially in crucial applications where the architectural honesty of the bonded components is vital.

Prevention Techniques Review
Given the destructive influence of porosity on weld high quality, efficient avoidance strategies are vital to keeping the structural stability of welded joints. In addition, choosing the proper welding parameters, such as voltage, current, and take a trip rate, can help lessen the threat of porosity development. By incorporating these avoidance strategies right into welding practices, the incident of porosity can be dramatically decreased, leading to stronger and a lot more trusted welded joints.Relevance of Correct Shielding
Correct protecting in welding plays an essential role in protecting against atmospheric contamination and ensuring the integrity of welded joints. Securing gases, such as argon, helium, or a combination of both, are generally used to secure the weld pool from responding with aspects airborne like oxygen and nitrogen. When these responsive elements enter call with the warm weld pool, they can cause porosity, leading to weak welds with minimized mechanical homes.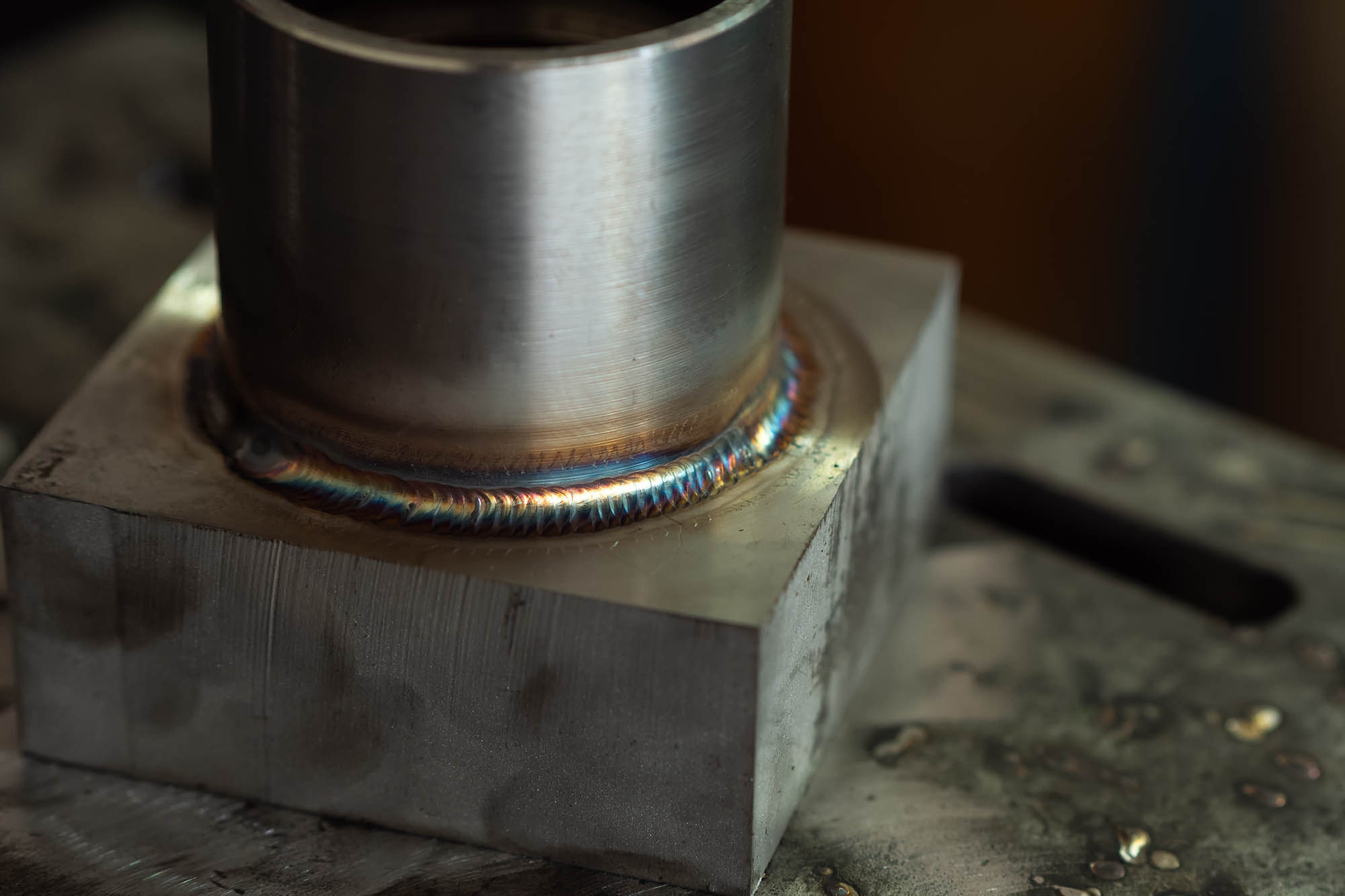
Inadequate protecting can result in various problems like porosity, spatter, and oxidation, jeopardizing the structural stability of the bonded joint. Adhering to correct protecting practices is essential to generate top notch welds why not try this out with very little flaws and make sure the long life and integrity of the welded elements.
Monitoring and Control Techniques
Exactly how can welders effectively keep an eye on and control the welding process to ensure ideal outcomes and prevent problems like porosity? One key approach is via making use of advanced monitoring technologies. These can consist of real-time tracking systems that offer feedback on criteria such as voltage, present, take a trip rate, and gas circulation rates. By continually checking these variables, welders can identify variances from the optimal conditions and make prompt adjustments go to avoid porosity formation.
In addition, implementing correct training programs for welders is important for checking and regulating the welding process effectively. What is Porosity. Enlightening welders on the value of keeping constant parameters, such as proper gas securing and travel rate, can aid stop porosity problems. Regular analyses and qualifications can additionally make sure that welders excel in tracking and managing welding processes
In addition, using automated welding systems can improve monitoring and control capabilities. These systems can specifically control welding parameters, reducing the chance of human error and ensuring regular weld high quality. By integrating innovative surveillance modern technologies, training programs, and automated systems, welders can properly keep track of and control the welding procedure to next reduce porosity problems and attain high-grade welds.
Final Thought
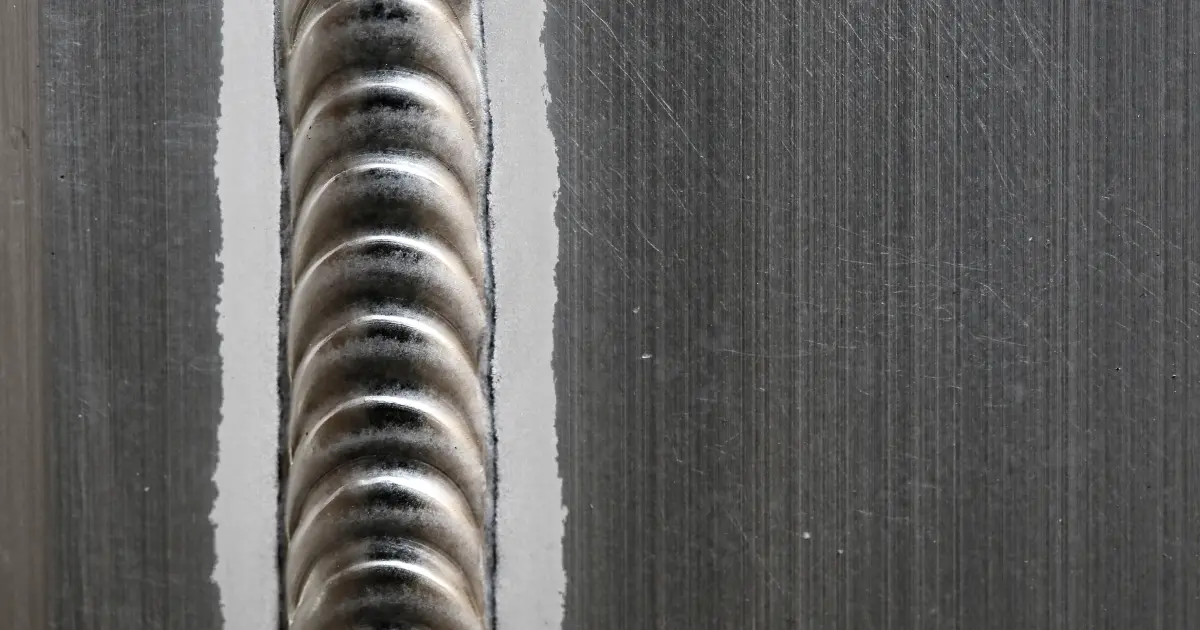
Report this wiki page